BACKGROUND
The aim of this work package is to improve maintenance cycles through so-called “Predictive Maintenance”. Predictive maintenance aims to ensure that machines and systems are proactively maintained when necessary, so that unplanned downtimes or quality losses are avoided. Unplanned downtimes cause irregularities, hectic activity, high costs and possibly orders that are delivered too late.
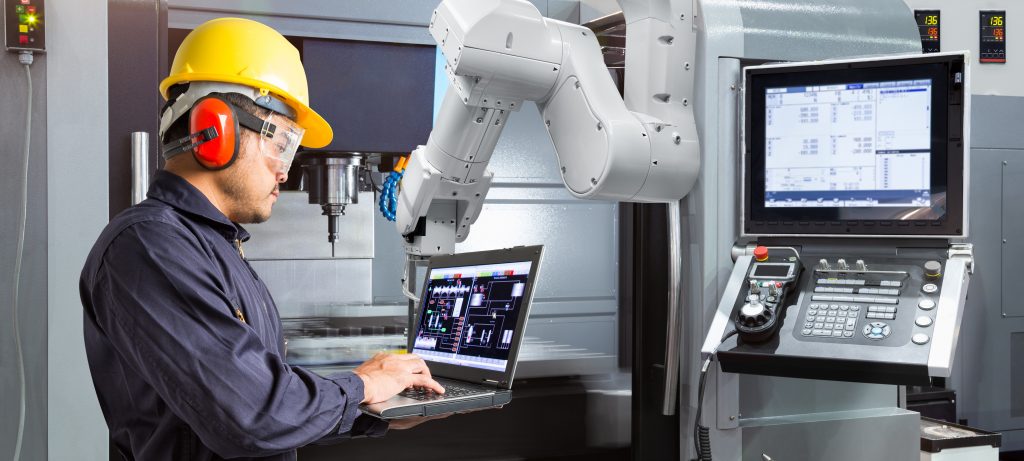
MODE OF OPERATION
The idea is based on the experience that changes, e.g. the aging of a machine, can be recognized by different perceptible phenomena. An example are machine operators of many years who can interpret these perceptions in sum with their experience. Multi-parameter measurements create the technical possibility of detecting information about changes in system behavior at an early stage. With the help of suitable sensory components for the detection of operating states, a multi-sensory subsystem is created via sensor fusion, which provides the necessary information for describing the operating state of the machine.
The linchpin is the regular flow of data, so that centrally collected data can be analyzed by algorithms in such a way that precise predictions of maintenance requirements are possible. Predictive maintenance is made possible by increasing digitization in companies as well as continuous improvement in sensor technology.
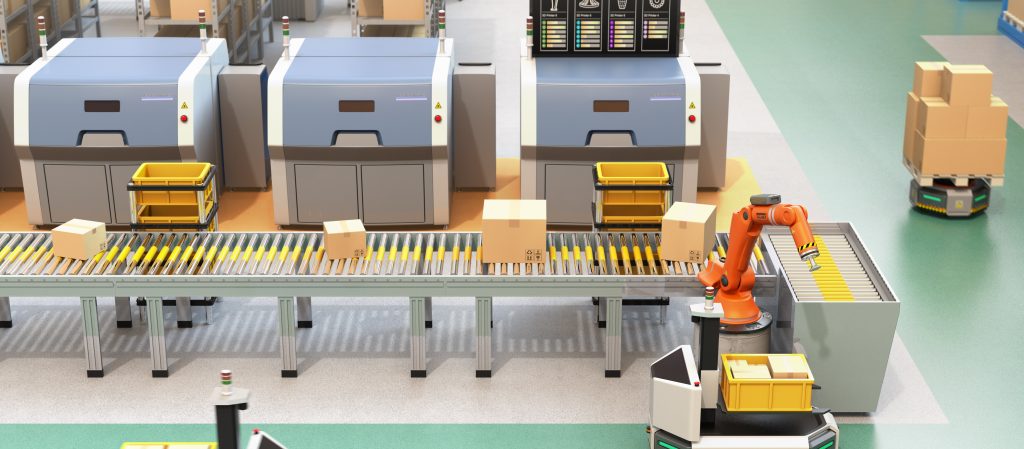
TECHNOLOGY
In order to be able to realize this vision, the following investigations will be carried out:
- Development and adaptation of an ultrasonic subsensor system
- Use of electromagnetic radiation
- Use of a radar for vibration detection
- Investigation of sensor fusion algorithms for use in embedded systems, particularly ultrasonic systems
- Evaluation of AI approaches to machine condition assessment based on multisensory data
- Analysis of “soft sensing” for “predictive maintenance” (combination of sensor values enable an additional parameter value or property of a system)
ADVANTAGES
Predicitve Maintenance as a possibility for cost savings
Experienced research partners (Prof. Berger, Prof. Hübner, IMI)
Sensor fusion can provide even more reliable predictions
Different machines can be investigated according to the modular principle
Low training effort for companies
Can be integrated into CMOS technology
APPLICATION
Industrie 4.0
STATUS
Design phase
CONTACT
Prof. Peter Langendörfer
Brandenburg University of Technology Cottbus – Senftenberg
Field of Expertise: Wireless Systems
Platz d. Deutschen Einheit 1
Room VG1C/1.30
03046 Cottbus
M: peter.langendoerfer@b-tu.de
T: +49 (0)335 5625 350